|
Sept WRAS Approval of EPDM Rubber
2017 -
TRP has been awarded the WRAS approval for its E293 EPDM Rubber compound. This further enhances the material offering that TRP has committed to, in bringing new approvals and materials to the market.
TRP’s Warren Febery commented, “this approval to the BS6920:2014 standard is yet another example of the high level of materials that TRP has to offer. We are constantly looking to our customers’ requirements in materials validation and will continue to seek approvals in line with both there’s and our needs”.
WRAS Material Approval is the testing of Non-metallic materials for use in drinking water. Materials undergo testing only for their effects on water quality. This type of approval demonstrates that the non-metallic material does not itself contaminate the water and therefore satisfies this particular requirement of regulations and byelaws. WRAS Approval is the easiest way to demonstrate compliance as it is granted directly by representatives of the water suppliers and is therefore accepted by every water supplier in the UK.
|
Sept Additional investment for the electricity distribution market
2017 -
TRP has invested in its second injection moulding press, and it has recently been installed and commissioned.
TRP’s Simon Children commented,
"This is a further investment – the first of two additional injection presses this year – in the market for electrical insulators, and represents our continued confidence in the sector. As we make further inroads in to the market, additional capacity is required to support the growing order book, as well as to satisfy significant end users that we have sufficient contingencies in our capacity to meet higher overall levels of demand."
|
Exciting new opportunities for TRP in China!
August 2017 -
TRP has achieved the Safety Registration Certificate for rubber gaskets for Plate Heat Exchangers issued by the CSCBPV (China Standardization Committee on Boilers and Pressure Vessels).
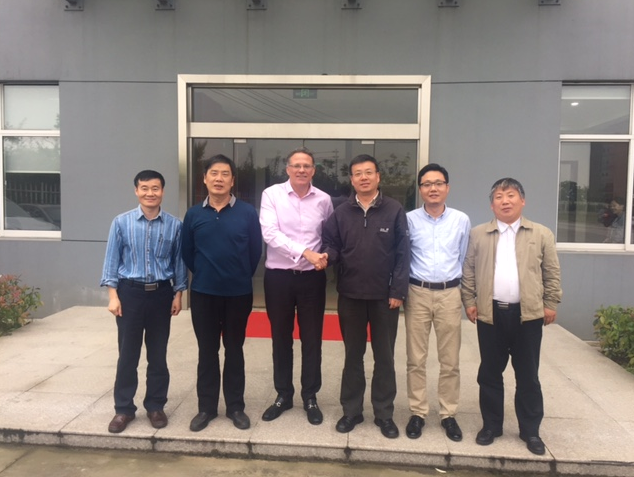
The certificate confirms that TRP’s systems and processes deliver high quality gaskets for use in Plate Heat Exchangers, and that TRP’s quality systems and materials are in accordance with the regulations specified by CSCBPV.
This means TRP Guangde can now manufacture and sell gaskets to the Chinese market, and TRP are one of only six gaskets manufacturers in China to have secured a certification.
This is an excellent accomplishment and is a great reflection on the team at TRP China.
From left to right: Bing Xu, Sales Manager TRP China, Mr Jin Fojia, Simon Children, TRP, Mr Zhou Wenxue, Secretary General of the CHEC and Professoriate Senior Engineer, Oliver Xu, General Manager TRP China and Zhao Liang, Secretary of CHEC.
|
July TRP Polymer Insulator Brochure
2017 -
TRP has launched its new Polymer Insulator Brochure containing useful data on the manufacturing of its range of insulators, their properties and technical advantages. http://www.trpinsulators.com/
Pete Smith commented 'This is another significant step in increasing our customers knowledge as to the range of products manufactured by TRP, and reflects TRP's growth in the non PHE sector.'
TRP has also doubled its injection moulding machine capacity in order to meet increasing world-wide demand for its insulators.
|
April Continued progress in the electrical insulator market
2017 -
TRP started the Year by making its first sales of 220 KV electrical insulators to the transmission sector.
This marked another positive development for TRP and follows on from its success in supplying the lower KV distribution insulator markets.
Simon Children commented ‘This is another significant step forwards for this range of product for TRP, and it reflects increasing confidence in TRP’s insulators serving this sector.’
TRP has also made the decision to invest in additional injection moulding capacity in 2017 to meet increasing demand for insulators.
After a significant investment in new plant, equipment and skills, TRP has started selling its first electrical insulators .
Polymer Matrix Composites (also called Polymer or Composite Insulators) were first introduced to the market in the mid-1970s. Over time these Insulators have demonstrated that they are a mature product with a potential life expectancy comparable to traditional porcelain and glass insulators. As such the polymer insulators are now being used at all voltage levels for both line and substation applications.
The main advantages of Polymer Insulators can be summarized as follows:
(a) Non-brittle and lightweight which helps lower construction costs;
(b) Ideal for use in compact line designs thereby reducing right-of-way and providing additional
construction cost benefits; and
(c) Superior seismic, safety and contamination performance.
These can be summarised in the table below:
Property | Porcelain | Polymer |
Strength | + | +++ |
Size | -- | ++++ |
Weight | -- | ++++ |
Breakage | - | +++ |
Aging Resistance | +++ | +++ |
Creepage/unit length | - | ++ |
Pollution Flashover | - | +++ |
Due to the inherent advantages of the Polymer Insulator product, the last years has seen a tremendous growth in India, China, Africa, Middle East and South America. In the case of Indian & Chinese market, Polymer Insulators have been extensively used with the primary goal of improving the pollution performance of the country’s power system. Only silicone rubber Insulators performed successfully and, for this reason, virtually all of the millions of composite insulators installed in India and China are today being made only from this silicone material.
Classification of Insulators
Following a review of this market, in 2014 TRP targeted this growing sector , and started the process of designing materials and processes to ensure it could manufacture product to pass the rigorous testing. Following a review of the market, in 2014 TRP targeted this growing sector in the market, and started the process of designing materials and processes to ensure it could manufacture product to pass the rigorous testing In early 2015 TRP submitted insulators suitable for lower voltage distribution for analysis and validation to the Central Power Research Laboratories of India and Electrical Research and Development Association, and following testing a preliminary approval was secured, and insulator product suitable for 11kV & 33kV applications has been sold to the market since October 2015. Insulators suitable for Higher and Extra High Voltage power applications have been submitted and approved by the KEMA Laboratories.
|
February 2016 - Phase 1 Refurbishment of its Hereford Site
TRP Sealing Systems has completed the first phase of the redevelopment of its offices and refurbishment of its Roe House building .
The updating and changes have involved the repositioning and modernisation of the offices to include accounts, production planning, customer service, production and purchasing.
The new layout has freed up production space that in turn has allowed for an improvement in production flow.
Further changes have allowed for new Laboratory and testing areas.
|
November 2015 - Silicone Injection Moulding
TRP Sealing Systems has recently taken delivery of a new 400 ton Desma injection moulding machine for the production of high voltage silicone insulators
The machine is equipped with an injection unit designed to handle paste silicone and is furnished with the necessary mould handling equipment to allow a range of insulators to be produced.
Tool trials are underway manufacturing a range of insulators from 11 kV to 400 kV
Simon Children TRP’s Managing Director commented
‘This is a new venture for TRP Sealing Systems that adds to our existing range of elastomer products TRP continues to look for and invest in new business opportunities.’
|
October 2015 - Large Rubber to Metal Bonding
TRP Sealing Systems Limited has completed its first order for large 100 Kg rubber to metal bonded components. The assembly consists of 5 items bonded together with a non-conductive elastomer.
Warren Febery TRP’s Technical Manager commented;
"this type of bonding poses special challenges as it is not possible to stress-relieve the areas of rubber in tension. Fortunately TRP’s understanding of the moulding process combined with the latest press technology has allowed us to overcome this potential problem."
The tooling used to manufacture the part was designed and produced in TRP’s own in-house tool-room. Formed in 1981, TRP is a specialist in precision elastomer engineering, and has a long history of innovation in materials, product design and processing. TRP is a privately owned company has an annual turnover in excess of £25 million (€32 million), and exports 95% of its products.
|
August 2015 - TRP start new venture in China
TRP is pleased to announce the opening of its new manufacturing facility in China in August 2015. TRP China is located in Guangde, Anhui province, and around three hours drive west of Shanghai.
The Project Manager for the operation, Ian Bell, commented “it has been a challenging but interesting journey in designing and building a facility to our specification, sourcing and installing all the necessary equipment and then recruiting a work-force. However, we are delighted with the management and operational team we have recruited and we have met our vision; commissioning a facility built and run to world-class manufacturing standards. There is still many things we need to work on, but we have made a great start, and the motivation and efforts of all the team in Guangde have been fantastic.”
The Asia-Pacific is a strategic market for TRP, and TRP has invested heavily in the new facility in China to best serve the domestic market and export markets. It will further help TRP to become the preferred partner for all advanced / technical rubber mouldings worldwide. With operations in the U.K., India and now China it will mean TRP have facilities and a strategy for each plant to best serve their local customer base, and a global footprint to support major engineering companies with a world-wide presence.
|
June 2015 - We’re cutting metal!
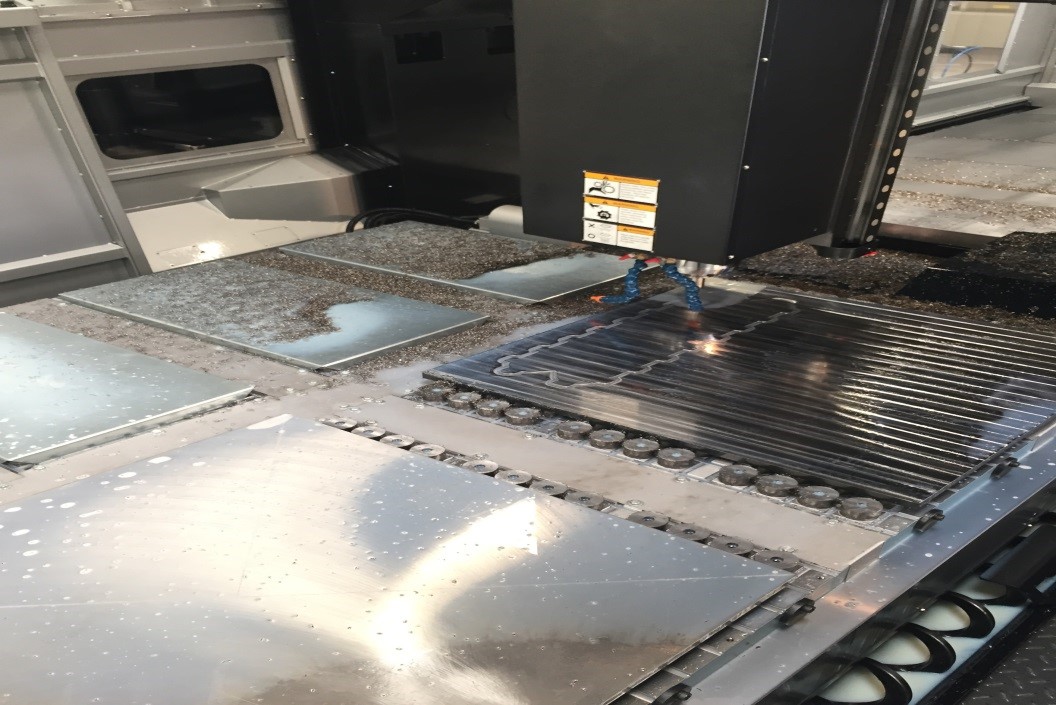

As part of its continuous investment programme, the CNC capacity has been installed at its Hereford facility in a purpose-refurbished tool-room that has been equipped with ancillary equipment to handle large and often complex components parts for its mould tools.
Engineering Manager, John Urbanski, commented "it had been an intense period of activity as we have prepared for, and installed the new machining capacity, as well as familiarised ourselves with the new software and programming requirements, but I am delighted we are now manufacturing the first mould on the machine"
TRP have the capacity and expertise to design and manufacture complex rubber mouldings weighing up to 50 kgs and mould tools up to 2m by 4m.
May 2015 - Additional Investment In Press Capacity For Fast Response Sampling

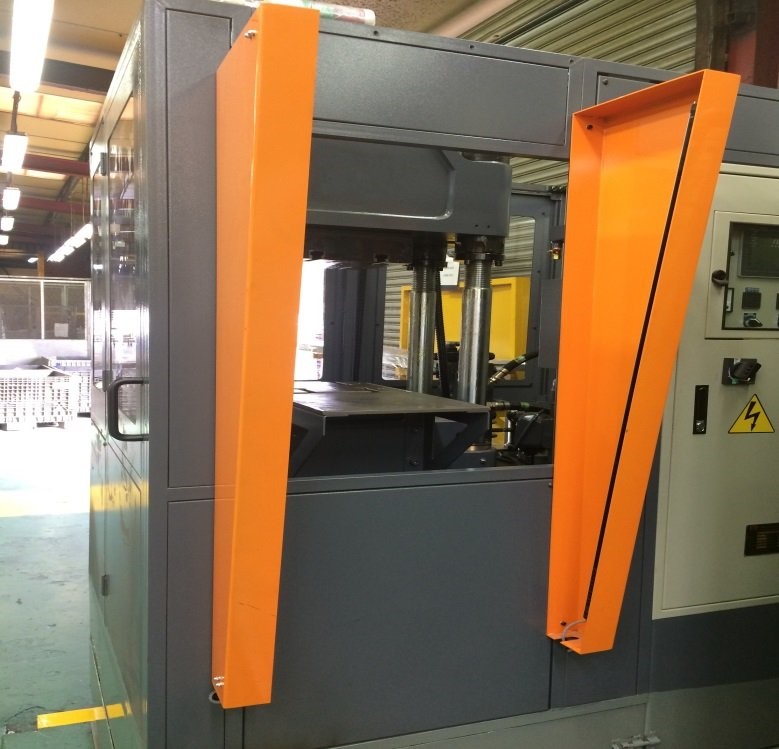
Peter Smith TRP’s Sales Executive for New Business Development commented:
Formed in 1981, TRP is a specialist in precision elastomer engineering, and has a long history of innovation in materials, product design and processing. TRP is a privately owned company, has an annual turnover in excess of £25 million (€32 million), and exports 95% of its products.
|
April 2015 - New CNC machine
TRP Sealing Systems is pleased to announce its investment in a new CNC machine for mould tool manufacture.
The CNC Machine is now installed and under commissioning at TRP. Simon Children, Managing Director, commented.
"We have already recruited a tooling engineer and we are ready to hit the ground running. Following machine commissioning we will start tool manufacture in June of this year.’ He went on ‘whilst I am sure we will continue to use our current mould tooling suppliers, our investment in internal capacity will further strengthen our supply chain, ensure greater flexibility and improved responsiveness.’"
In addition to its investment in the new machining centre and software TRP Sealing Systems has re-housed its entire tool-room to a newly refurbished building containing all of the ancillary equipment necessary for handling such large tools.
|
Jan 2015 - TRP release a range of Case Studies
|
Aug 2014 - TRP moulds a two metre seal to +/- 1 mm
TRP are producing moulded elastomer seals valve seals over 2000 mm Dia. Possibly more impressive is the fact that the tolerance is just 2 mm. Produced on TRP's range of modern computer controlled moulding equipment has allowed this degree of precision that would normally be associated with much smaller components.
"Our understanding of elastomers and our ability to control our processes and
production environment has allowed us to accurately predict the finished size," said TRP Technical Manager Warren Febery, "Our customers can rely on TRP to provide product to meet the increasing technical demands required by our industry."
|
Aug 2013 - New Presses allow for expansion of automotive production
Responding to continued demand within the automotive sector,
TRP has added a further two 700 ton up-stroking moulding machines. This additional capacity has allowed TRP to capitalise on customer needs for consistent quality mouldings.
TRP Production Manager Nick Garrett commented “with our continued investment in high quality new equipment we are now in a privileged position to have some of the most modern production equipment in the rubber moulding industry”.
The first components produced on the new presses were for a leading first tier supplier to JLR. Their spokesman commented “with the increasing demand for fast turnaround and short lead-times TRP’s continuous operations and standardisation of equipment provides the response we need to maintain our commitment to the automotive industry”.
May 2013 - TRP Sealing Systems turns up the heat
“With elastomers expected to operate within a greater temperature range and coming into contact with more aggressive chemicals, new and existing customers are turning to TRP to overcome problems that have frustrated our competition.” said TRP Technical Manager Warren Febery. “We are also providing additional development capacity to meet market growth in the near term.”
TRP's activities include the design and production of elastomer mouldings from product design and process engineering through to prototype and full production. This is based on its extensive knowledge of rubber moulding, rubber to metal bonding and combining rubber with PTFE.
Feb 2013 - TRP Sealing Systems expands production capacity with new compression moulding press
Responding to a steady increase in customer demand, TRP has expanded its production capacity with the acquisition of a new 700 tonne compression moulding machine.
The new 950 mm x 1,830 mm upstroke compression moulding press will enable the Hereford based elastomer moulding company to cut lead times, and this new acquisition in equipment completes a line-up of 18 identical presses, and complement TRP’s range of presses from 25 to 1,200 tons.
“With strong and continuing growth in our order book, the new press will enable us to improve our responsiveness” said TRP's Managing Director Simon Children, “and it will also provide additional capacity to meet market growth in the near term.”
The press provides a range of advanced features including full electronic control and even heat distribution from its oil heated platens. TRP's activities in the design and production of elastomer mouldings range from product design and process engineering through to prototype and full production. This is based on its extensive knowledge of rubber moulding, rubber to metal bonding and combining rubber with PTFE.
Jun 2012 - TRP business boom after expanding into the Indian market
A HEREFORDSHIRE businessman is to share some of his tips for export success at a breakfast event later this month. Simon Children, managing director of TRP, has seen business boom after expanding into the Indian market.
He will be talking about what he has learnt about working with India at the breakfast briefing, Doing Business with India, on April 25. TRP, which designs and manufactures sealing systems for global blue chip engineering companies, was set up by Mr Children’s father Peter Children in 1981.
The £26m turnover business has grown to the point where it now exports 99% of what it produces and in addition to the UK, has operations in India and Romania. Simon Children, who originally trained as a lawyer but returned to the family business after working for 10 years in London, said: “Our customers are mainly in the oil and gas field, the ship building industry, the food and drink sector and the nuclear industry. “All of them have approached us to design and manufacture new sealing applications. Our growth has been down to the fact that every single application requires a specific design to solve a unique problem.
“Because we have been trading for over 30 years we already have a catalogue of materials which allow us to meet almost all our customers’ needs. But with technology ever evolving, we must remain ahead of the game by developing new material for upcoming applications – so we are growing and expanding our product range all the time.” The firm started working in India three years ago because the company was growing and looking for a manufacturing strategy which would help the firm expand.
The business has been helped by the fact there are only three companies across the globe which does what it does - two of which are in Sweden. “The market in India was attractive, not only because of its competitive labour costs, but because it was a faster growing market than its counterparts in Europe,” he added. All of TRP's corporate functions are still managed in the firm’s Hereford base, including the whole corporation’s financial operations, and all material design and testing. In the UK it employs around 300 people; 120 in India and 100 in Romania. The Romanian site is a service facility for the UK operation, but in India all manufacturing processes are on one site.
“Clearly the Indian and Asian markets are growing. If UK firms and West Midland businesses don’t get out there our competitors will,” said Mr Children. “I saw working with India as a crucial strategic step to grow the business. Any company that wants a global footprint must start looking at working with India, China or Asia – or all three.”
|
Jun 2012 - TRP add additional test equipment
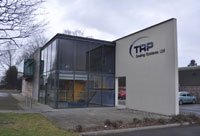
TRP are pleased to announce that they have added the latest advanced tensometer for use in their technical centre. The new tensometer will be used to audit products produced at their Hereford site.
The new equipment sends the test results directly to the on-line quality system, ensuring the accurate updating of data and the monitoring of production trends.
In addition, the tensometer will be used along with other test and analytical equipment to support the development of new materials and products.
|
May 2009 - TRP expansion into India
Established in 2009, TRP Sealing Systems (India) Pvt is already producing 30% of TRP’s global demand and is able to achieve direct supply into Asian markets.
Supported by our UK team of engineers and applying all of the best manufacturing and quality procedures of the Hereford factory, TRP (India) expects to continue to grow and develop to meet the needs of expanding world markets.
|
Aug 2008 - TRP receive the Queen's Award for Enterprise

|